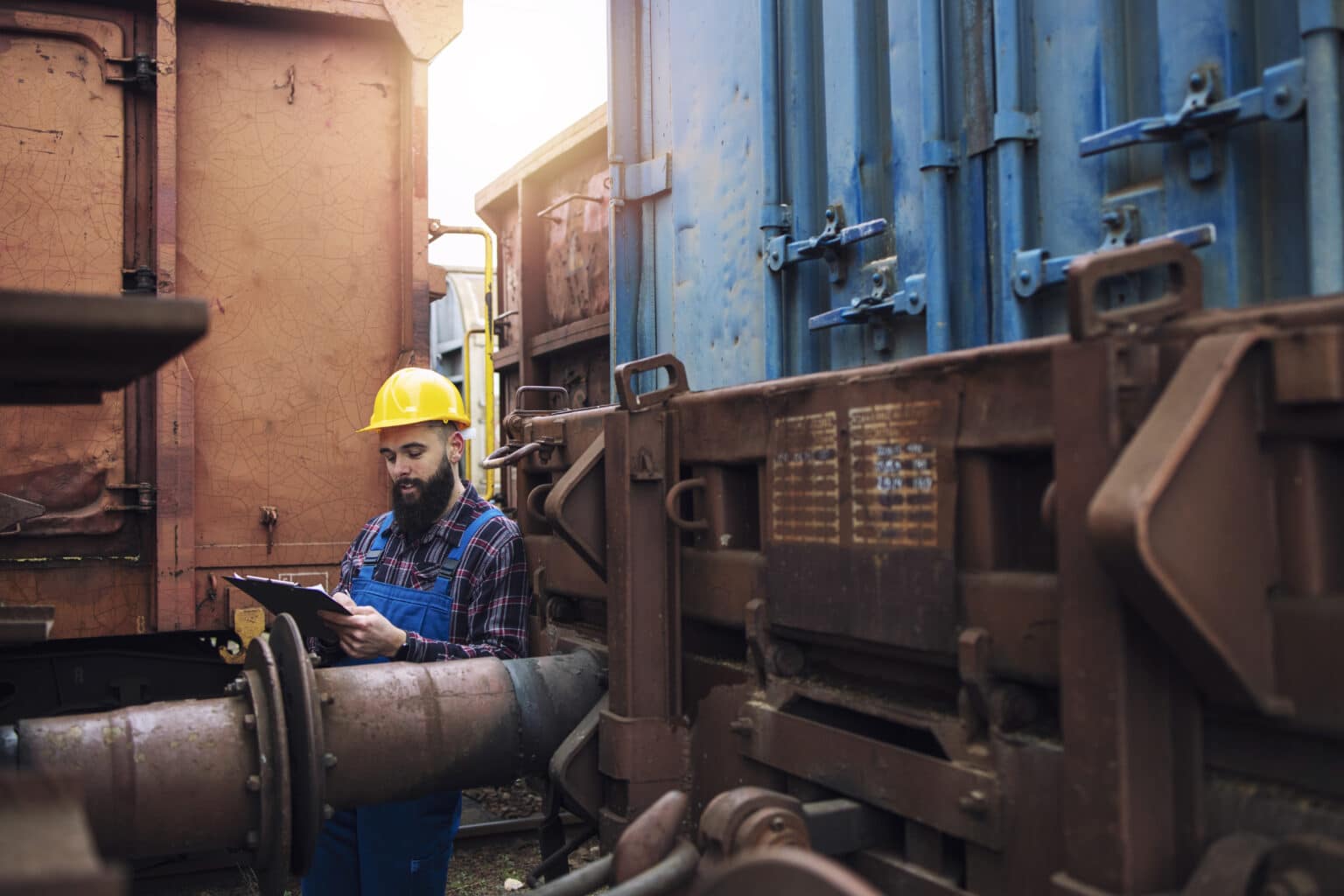
Types de pannes de machines industrielles et causes
Les machines industrielles sont au cœur de nombreuses opérations de fabrication, et leur bon fonctionnement est essentiel pour garantir l’efficacité et la productivité. Cependant, les pannes des machines industrielles sont inévitables et peuvent avoir un impact significatif sur la production. Il est essentiel de comprendre les types de pannes et leurs causes pour minimiser les temps d’arrêt et prolonger la durée de vie des machines industrielles. Dans cet article, nous allons explorer les types de pannes les plus courants et les causes de ces défaillances, en fournissant un aperçu détaillé de la manière de prévenir et de gérer ces problèmes.
Types de pannes dans les machines industrielles
Chaque panne de machine industrielle peut être classée en fonction de la nature de ses problèmes. Selon le type de machine ou son fonctionnement, on trouvera différents types de pannes.
Pannes mécaniques
Les pannes mécaniques sont l’un des types de pannes les plus courants dans les machines industrielles. Ces pannes peuvent être causées par l’usure naturelle des composants mécaniques due à une utilisation continue et à un manque d’entretien adéquat. Une lubrification incorrecte ou insuffisante peut provoquer une surchauffe et endommager les pièces mobiles, ce qui affecte directement la durée de vie de la machinerie. Chez Nortek, nous vous offrons le service dont vous avez besoin pour automatiser vos processus de lubrification industrielle.
En outre, une mauvaise utilisation et une charge excessive sur les machines peuvent entraîner des pannes, provoquant l’usure des composants plus rapidement que prévu. La réparation de ces défaillances mécaniques nécessite souvent une intervention technique spécialisée, qui peut être coûteuse et prendre du temps.
Défauts électriques
Les pannes électriques dans les machines industrielles peuvent inclure des problèmes avec les composants électriques tels que les moteurs, les câbles et les systèmes de contrôle. Ces défaillances peuvent être dues à l’obsolescence des machines, à l’utilisation de composants défectueux ou à une maintenance inadéquate. L’absence de plan de maintenance préventive peut permettre à des problèmes mineurs de s’accumuler et d’aboutir à des pannes électriques plus graves. En outre, des erreurs dans le logiciel ou la programmation des systèmes de contrôle peuvent également provoquer des interruptions dans le fonctionnement des machines. Pour éviter ces pannes, il est essentiel d’effectuer une maintenance régulière et de s’assurer que tous les composants électriques sont en bon état.
Défaillances hydrauliques
Les pannes hydrauliques constituent un problème important pour les machines industrielles dont le fonctionnement repose sur des systèmes hydrauliques. Ces défaillances peuvent être dues à un manque de lubrification, à l’utilisation de lubrifiants inappropriés ou à l’usure des surfaces internes des composants hydrauliques. L’absence d’entretien régulier peut permettre l’accumulation de contaminants dans le fluide hydraulique, ce qui peut endommager gravement les pièces internes. En outre, le mauvais fonctionnement des vannes ou des pompes hydrauliques peut perturber les processus industriels et entraîner des pannes graves. La mise en œuvre d’un plan de maintenance approprié et la surveillance régulière des systèmes hydrauliques peuvent contribuer à prévenir ces défaillances.
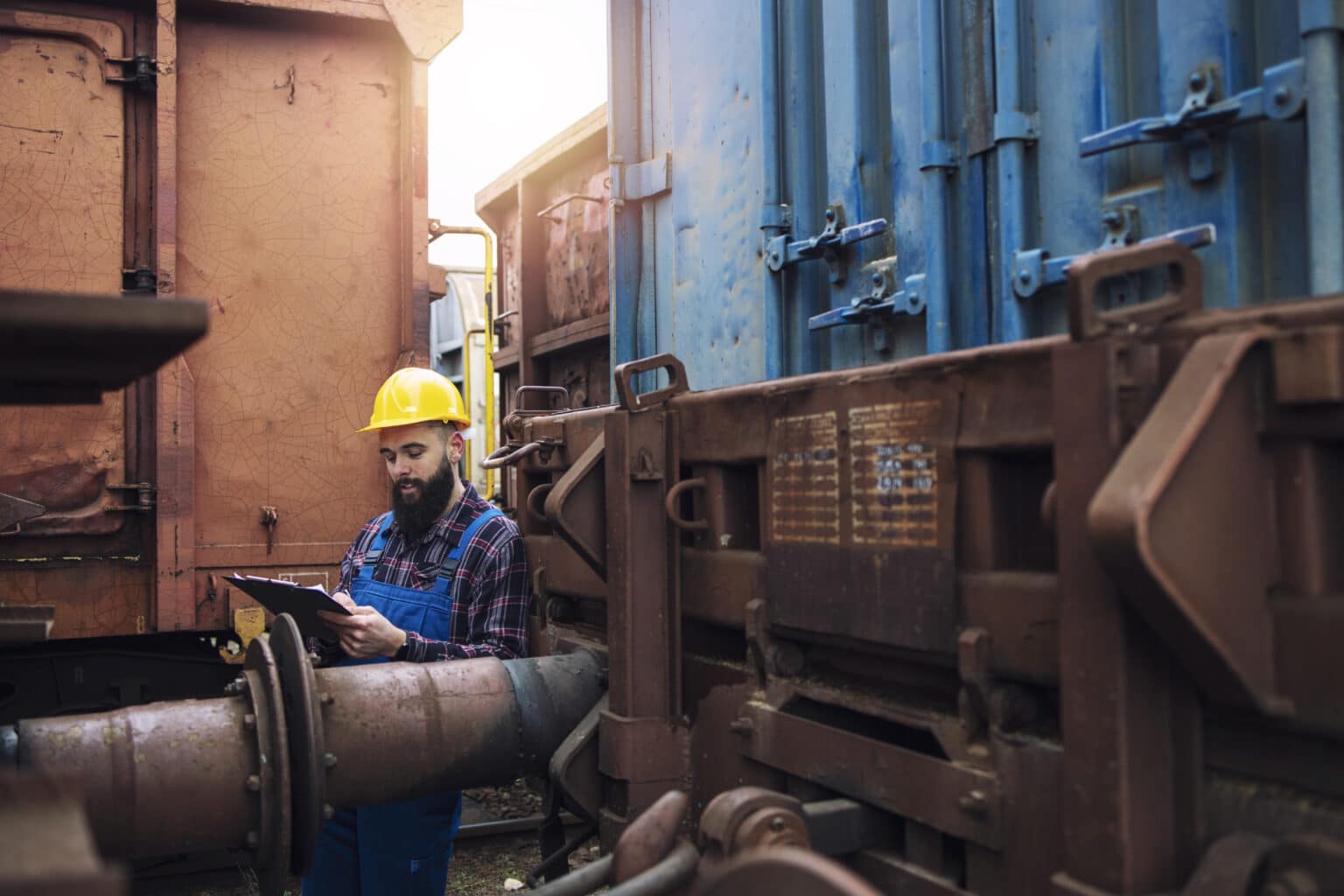
Pannes pneumatiques
Les pannes pneumatiques surviennent dans les machines qui utilisent de l’air comprimé pour fonctionner. Ces systèmes peuvent tomber en panne en raison de l’obstruction des conduites d’air, de fuites ou de l’usure des composants pneumatiques. Le manque d’entretien et l’accumulation d’humidité dans le système peuvent provoquer de la corrosion, endommager les pièces internes et réduire l’efficacité du système. En outre, une utilisation continue sans supervision appropriée peut entraîner une usure accrue et une défaillance de l’équipement. Pour minimiser ces problèmes, il est essentiel de procéder à des inspections régulières et de maintenir le système pneumatique propre et bien lubrifié, afin de garantir ses performances optimales.
Causes de défaillance des machines industrielles
Bien que la nature des échecs soit souvent aléatoire, nous pouvons trouver certaines habitudes ou certains événements qui conduisent régulièrement à des échecs.
Manque d’entretien
Le manque d’entretien est l’une des causes les plus fréquentes de pannes des machines industrielles. Lorsque la maintenance préventive n’est pas effectuée correctement, des problèmes mineurs peuvent s’accumuler et déclencher des pannes plus graves. L’absence d’un plan de maintenance structuré peut augmenter le risque de surchauffe et d’usure prématurée des composants. En outre, le fait de négliger la lubrification et l’entretien des systèmes peut entraîner des défaillances mécaniques et électriques.
Usure des composants
L’usure des composants est une conséquence naturelle de l’utilisation continue des machines industrielles. Au fil du temps, les pièces mobiles et les composants critiques subissent des frottements et des contraintes qui peuvent entraîner leur défaillance. L’absence d’un programme de maintenance correctement mis en œuvre peut accélérer cette usure, en particulier si la lubrification des pièces n’est pas effectuée régulièrement. L’usure peut également être exacerbée par une mauvaise utilisation des machines ou une surcharge. Pour minimiser l’impact de l’usure sur les machines, il est essentiel de procéder à des arrêts réguliers et de remplacer les composants endommagés avant qu’ils ne provoquent des pannes majeures.
Erreurs humaines
L’erreur humaine est une autre cause importante de défaillance des machines industrielles. Un manque de formation adéquate, une supervision insuffisante ou une étourderie occasionnelle peuvent entraîner une mauvaise utilisation des machines, ce qui peut causer des dommages irréversibles. Les opérateurs peuvent mal programmer les systèmes ou ignorer les signaux d’alarme sur les machines, ce qui entraîne des dysfonctionnements. En outre, la pression exercée pour respecter les délais de production peut conduire à des raccourcis qui compromettent la sécurité et les performances des machines. La mise en œuvre de programmes de formation continue et une supervision stricte peuvent contribuer à réduire l’incidence des erreurs humaines et à améliorer la fiabilité des machines.
Obsolescence planifiée
L’obsolescence programmée est une stratégie de conception dans laquelle les fabricants programment la durée de vie utile de leurs produits de manière à ce qu’ils deviennent obsolètes après un certain temps. Dans le contexte des machines industrielles, cela peut entraîner une augmentation des pannes, car les machines sont conçues pour tomber en panne au bout d’un certain temps. Cette pratique peut entraîner une augmentation des coûts de réparation et de remplacement pour les entreprises et perturber les processus industriels. Pour lutter contre l’obsolescence programmée, il est essentiel que les entreprises investissent dans des machines de haute qualité et établissent des relations avec des fabricants qui privilégient la durabilité et l’assistance à long terme.
L’importance d’éviter les pannes de machines
La prévention des pannes des machines industrielles est essentielle pour maintenir l’efficacité opérationnelle et réduire les coûts associés aux réparations et aux temps d’arrêt. Les pannes n’affectent pas seulement la production, mais peuvent également compromettre la sécurité des travailleurs et les délais de livraison. La mise en œuvre d’une maintenance industrielle appropriée, ainsi que d’un plan de maintenance préventive, peut aider à identifier et à résoudre les problèmes avant qu’ils ne se transforment en pannes graves. En outre, l’investissement dans la formation des opérateurs et la mise à niveau des équipements obsolètes peuvent minimiser le risque de pannes. En fin de compte, la prévention des pannes des machines industrielles joue un rôle clé dans l’optimisation des processus de fabrication et la réussite de toute entreprise.